The blades from a wind turbine consist of a composite material that makes it hard to recycle them. But researchers are working on it.
Wind turbines are designed to last at least 20 years. However, they may often work far beyond their estimated service life if properly maintained. Sooner or later, however, they will be so marked by wind and weather that they must be taken out of use. And that time has now come for the first large generation of energy-producing wind turbines.
Most parts of the turbine can be reused without problems. Reuse is more problematic when it comes to blades made of composite materials consisting of glass fibres held together by a strong glue like epoxy. According to a statement from the European Technology and Innovation Platform on Wind Energy (ETIPWind), there will be around 66,000 tonnes of end-of-life wind turbine blades in Europe in 2025, and intensive work is currently being done to find out how they can be given new life rather than simply being deposited in landfills. It is, in fact, not a very good idea to incinerate them as ordinary waste, because it leaves a lot of ash and many fiberglass particles.
Development Engineer Justine Beauson is a materials scientist at DTU. For several years, her field of research has been what to do with end-of-life wind turbine blades. For example, Justine can describe how wind turbine blades—or various parts of them—have been used as exciting structures in playgrounds and— in crushed form—as reinforcement in concrete, as fillers in noise attentuation screens, and the like.
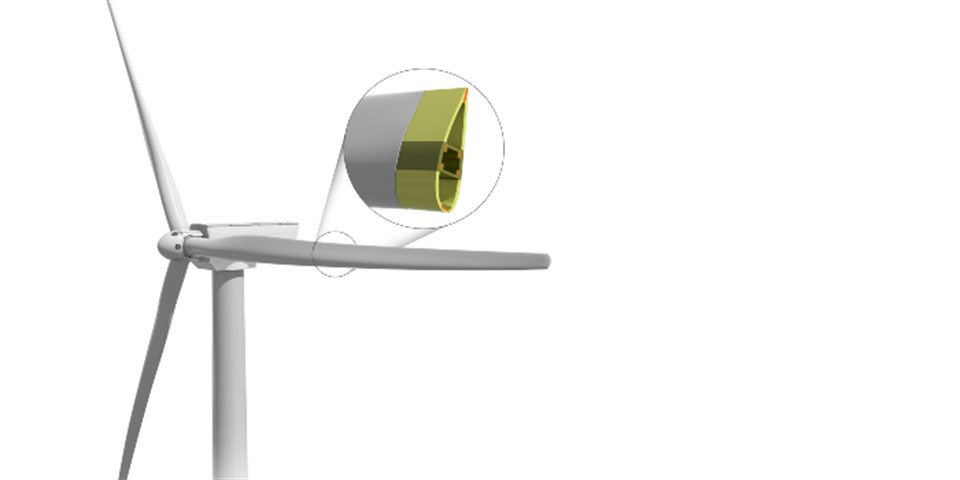
Structure of a wind turbine blade
The places on the blade that are subject to the greatest strain (dark green areas) consist of a composite material made of parallel strong glass fibres bound together by a plastic material such as epoxy. The light green places consist of a core of balsa or a foam plastic material, surrounded by a thin layer of plastic composite. These parts must be light and also very rigid, so that they can maintain their shape when the wind affects them because the effect of the wind turbine depends greatly on the carefully designed aerodynamic blade profile.
"But—at the end of the day—these creative ideas won’t be enough to solve the problem. You can build play equipment from the blades for a while, but—at some point—these will also need to be recycled. And there will still be many blades for which we need find other uses. Wind turbines are—in fact—naturally associated with sustainability, and we therefore also need to find sustainable solutions to the problem of how to dispose of them as waste,” she says.
A complicated structure
Justine and her colleagues at DTU are working with the problem from several angles; both how the material is to be processed to get the most valuable product for reuse, and whether the current formula for materials for wind turbine blades can be changed, so that they become easier to recycle or even biodegradable.
A wind turbine blade is an ingenious composition of different materials, carefully designed according to the load to which the individual parts are exposed and how to get the maximum energy yield from the blade (see Figure above).
The entire composite structure of a blade is not easy to disassemble when it has reached its end-of-life and should preferably form part of a cycle rather than ending up in a landfill. This can be done by cutting the blades into smaller parts and exposing them to temperatures of minimum 450 degrees—so-called pyrolysis—where the epoxy is burnt off. But the strength of the glass fibres is reduced in this process.
“In the original blade, the glass fibres are located neatly side by side throughout the length of the blade, but when you divide the blades into parts and then break it down using pyrolysis, the fibres obviously become shorter and will be unevenly distributed. It’s an expensive process, which also impairs the quality so that the fibres cannot be used for new blades. In turn, they may possibly be included in fiberglass products for trains and cars, for example,” says Justine Beauson.
“Using a chemical process, you can preserve more of the good properties of the fibres. However, the chemical substances are difficult to recycle and not very environmentally friendly. In addition, the process must take place in a high-temperature and high-pressure reactor, which means that the process is overall more expensive and less sustainable than pyrolysis.”
Long road to a sustainable solution
Fiberglass composites are thus not a very recyclable material. So perhaps another alternative path should be explored. Justine and her colleagues are also working on this. For example, one project—Bio4Self— has created a lot of attention. Here, the idea was to circumvent the problem of disassembling the components by creating a composite material based on a single plastic polymer (PLA), which—as an added bonus—is extracted from agricultural production waste and is biodegradable.
Unfortunately, the PLA material is too brittle for blades, but the researchers have not given up the idea of developing usable biocomposites, perhaps with bamboo fibres.
A more radical solution that Justine has in mind is that you could use enzymes to ‘eat’ the plastic polymer when the blade has come to the end of its life. But much research is required to get there, if it is at all possible.
DTU is part of several networks—both Danish and international—which focus on recirculation of wind turbine blades.
In DecomBlades—a large Danish project supported by Innovation Fund Denmark—ten industry and research partners have joined forces to create sustainable and cost-effective solutions. The aim of the project is to test and scale up the above three methods: mechanical crushing, use of crushed blade material for cement production, and pyrolysis.
“At present, none of these solutions meet all the requirements that can rightly be made in relation to environment, safety, and price. So I think we need to find a suitable mix of them all. But we must also still work with the whole chain, from materials and manufacturing processes to reuse and recycling. There’s still some way to go,” says Justine Beauson.