'WaveTouch' is the name of a new type of touch screen based on optical technology. The screen is both better and cheaper to produce than screens on the market today. Developed at DTU, it is now ready to conquer the world market.
Together with the electronics company OPDI Technologies A/S, researchers from DTU Fotonik have developed the new screen which is controlled by optical technology. The screen is cheaper to produce and in several ways outperforms the monitors we know from smartphones and tablet computers. Backed by an investment of DKK 17 million and sophisticated production equipment from a Chinese company, the touch screen of tomorrow is now ready to conquer the world market.
The idea for a brand new type of touch screen came about in 2007 as the CEO of OPDI Technologies, Jørgen Korsgaard, had grown tired of the touch function of his recently acquired cooker not working whenever its surface became wet—which obviously is inappropriate for a cooking device. The researchers at DTU took up the challenge, and as the first iPhone with touch screen at the same time was winning over millions of consumers worldwide, it seemed only natural to focus on developing a solution that could be used in all types of touch-controlled products. Thus, the researchers recently were able to present a prototype of a fully functional optical screen with very promising export potential.
Optical control
The optical screen–which has been named WaveTouch—uses laser as its light source. The laser source emits light from one of the screen corners and the light then hits an embedded diverging lens which reflects the light across the plastic plate—the functional part of WaveTouch (see figure). A micro camera is located in the corner opposite the laser source, and this camera detects the point of finger position based on the transmitted light in the plastic plate. When your finger hits the touch screen, the laser light is interrupted and the camera is then able to pinpoint exactly where in the integrated coordinate system the interruption occurred. This is translated into a pulse which is recorded on the screen. The function is therefore completely comparable to how you operate a standard smartphone screen, but light moves across the screen instead of electrons.
Works under water
In the laboratory at DTU Fotonik, Senior Researcher Henrik Chresten Pedersen is preparing a demonstration of WaveTouch. Together with Senior Researcher Michael Linde Jakobsen and Research Specialist Steen Grüner Hanson he is part of the team that has invented the new screen technology. Right now, the prototype housing the WaveTouch technology most of all resembles a lunch box, but—as we know—looks can be deceiving. This becomes very clear when Henrik C. Pedersen pours water into the ‘funnel’ and then slides his finger across the water-covered touchpad after which the letters ‘DTU’ appear on the display– a touch screen functioning under water has been born. Without further adjustments, the screen can be used in the rain whereas other monitors will cease to work. This means that the new screen would be a natural component in interfaces in, e.g., outdoor digital information boards.
Competitive production price
Screens for traditional smartphones and tablet computers consist of several glass layers that are built up in a ‘sandwich structure’ with other layers of thin, transparent metal grilles being placed in between the glass parts. When you touch the top glass, the electrical properties of the metal layers change, thus creating the necessary pulse. However, it is expensive and difficult to produce screens with metal and glass layers and the error rate is high, so many of today's screens have to be scrapped during production. Henrik C. Pedersen explains that because the WaveTouch screen uses laser light, it can be built up of just a single layer cast plastic:
“WaveTouch is therefore significantly cheaper to produce than other types. Furthermore, the metal layer in standard smartphone screens has a high content of the rare element indium which is suitable for producing transparent electrodes, but which has become a very scarce resource. Indium is expensive, and Chinese electronics companies have already purchased most of the world's known indium reserves. We can therefore expect an even higher cost price on standard screens in future.”
Scaling benefits and improved signal reception
In terms of size, the traditional screen manufacturers are also facing a problem: “The immense complexity of the glass and metal layer structure means that the greater the ‘sandwich screen’, which must be designed, the greater the risk of errors during production. The WaveTouch screen, however, can be scaled to all sizes. It only requires changing the mould to produce either a screen for a pocket camera or a screen the size of a cinema screen, and the risk of error is not significantly greater with major products,” says Henrik C. Pedersen. And WaveTouch has another advantage to ordinary screens:
“Since metal can easily disrupt wireless signal reception, smartphone antennas must be placed around the screen in order to function, which presents a number of design-related challenges and reception is still not always optimal. The WaveTouch technology works in plastic-moulded monitors, which enables a range of entirely different design solutions to which DTU Fotonik will be providing input. The finished units which are based on the WaveTouch technology are expected to have better signal reception and GPS functions than similar traditional screens,” says Henrik C. Pedersen.
Costly plastic moulding
It sounds almost too good to be true and according to the researcher there is indeed a significant obstacle to the global breakthrough of the WaveTouch technology:
“When designing the prototype, we found out that tailored plastic production moulds are extremely expensive. The mould alone for our prototype costs around DKK 300,000. OPDI will now present finished specific prototypes to its customers and it is, of course, best if the prototype can be produced at relatively low costs. For this reason, DTU Fotonik, OPDI and other business partners have started a project which aims at reducing production costs for Danish plastics companies,” concludes Henrik Chresten Pedersen (see fact box).
Of the seven patents that form the core of WaveTouch, five are pure DTU patents developed by DTU Fotonik. The last two patents were developed by OPDI.
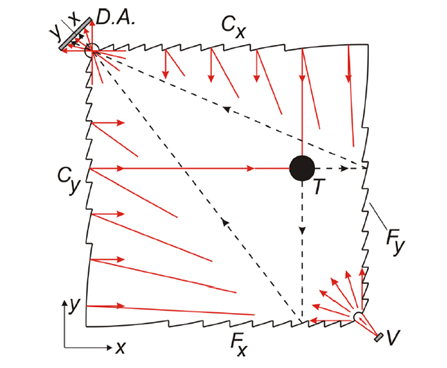
The laser source (V) emits light that is intercepted by embedded reflectors (C and F).
Light is distributed across the specially designed plastic construction where it is intercepted by a camera (D.A).
The data are translated into points in a coordinate system.
When a finger touches the screen (T is the touch point), the beam is interrupted and this is ‘translated’ into a pulse on the display